アフターサービス
AFTER SERVICE
After-sale service of Miroku machine
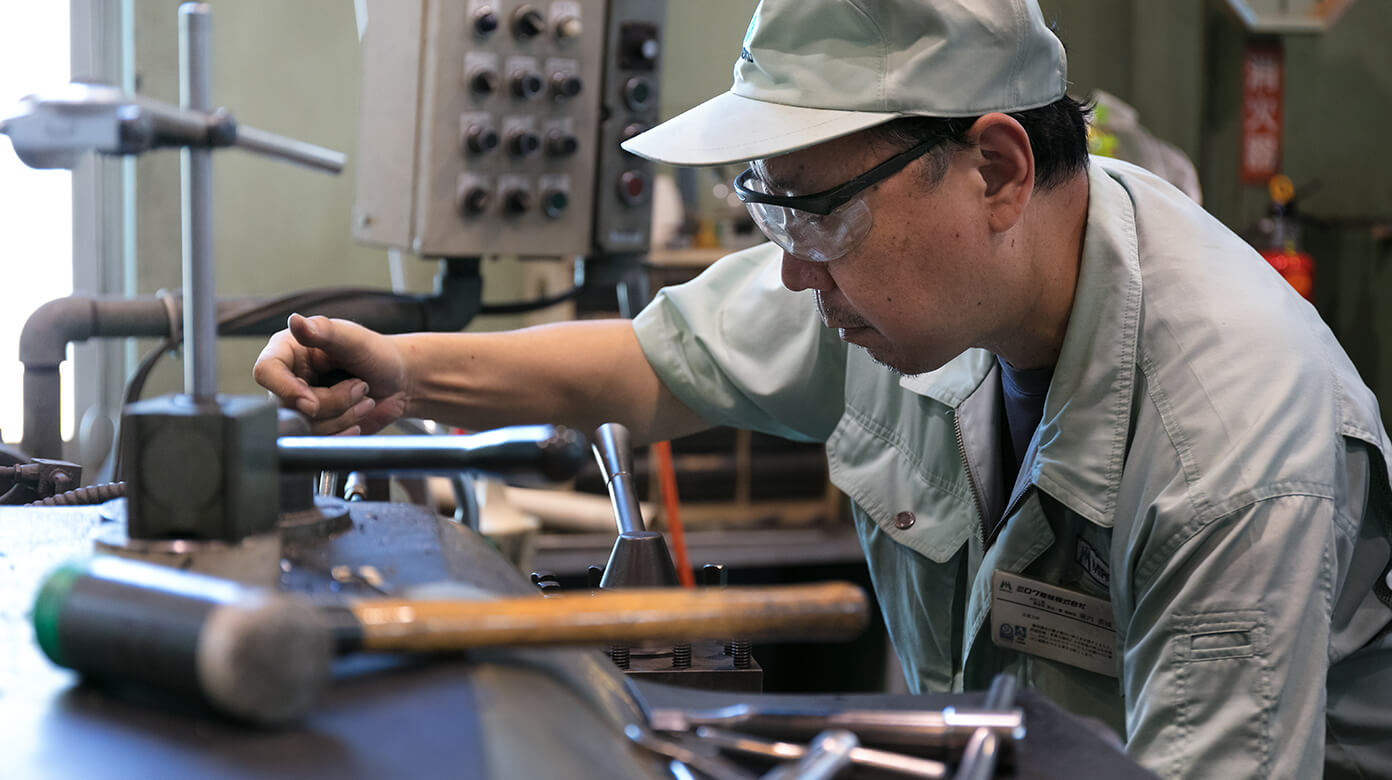
We believe that after-sales service is also part of the product. In order to maintain performance and productivity and to be able to use it for a long time, Miroku Machinery has an after-sales service system that guarantees peace of mind.
Maintenance with the know-how accumulated over a long period of time and the skill of the craftsman. We will follow regular patrols and dispatching of technicians by sales representatives, and will keep track of the machines introduced.
Trouble Shooting
Guide on Gundrilling
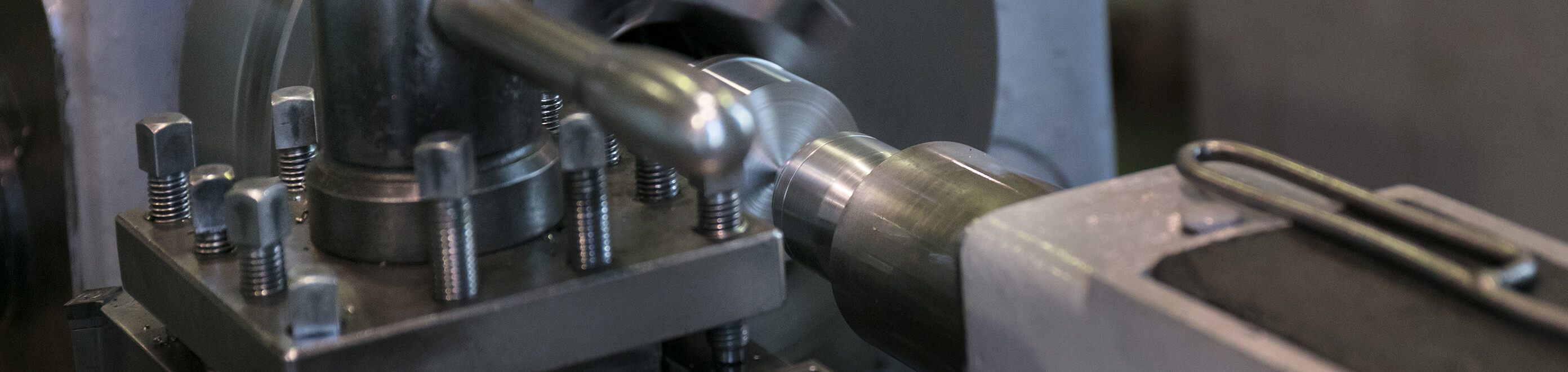
CASE01Tool failure
Time of failure
Cause
Countermeasure
- Hole to entrance
-
- Machine
-
- Check if the feed is properly set
- Check if part is properly clamped
- Check if whip guide is properly set
- Tool
-
- Check if tip is properly sharpened
- Drill bush
-
- Check if there is oil leak or entangled chips
- Hole midway
-
- Machine
-
- Check if the head is evenly fed
- Damaged tip
-
- Refer toTool Life section
- Hole exit
-
- Cutting Feed Rate
-
- Reduce cutting feed rate at hole exit
- In retract
-
- Part shape
-
- Check for hole curves at exit caused by inclined endface of part
- Burnishing torque
-
- Reduce the cutting speed
CASE02Tool life
Trouble
Cause
Countermeasure
- Poor tool life
-
- Improper machining Variables
-
- Check if the speed is properly set
- Check if cutting feed rate is proper
- Machine
-
- Check if the spindle run out is excessive
- Check if the spindle and drill bush are properly aligned
- Check if the guide bore of drill bush is worn beyond limit
- Check if whip guides are properly set
- Tool
-
- Check if proper nose angles or guide pads are selected
- Check if the drill OAL is proper
- Check if the drill is properly reground
- Coolant
-
- Check if proper coolant is used
- Check if coolant is properly filtered
- Check oil temperature. Change to a tank of larger capacity if necessary
- Work material
-
- Is there no unevenness in the material?
CASE03Machining accuracy
Trouble
Cause
Countermeasure
- Poor surface finish
-
- Improper cutting feed rate
-
- Reduce cutting feed rate
- Machine
-
- Check for spindle runout, erratic feed oversized bush bore, clamping error
- Tool
-
- Check if drill is firmly secured
- Coolant
-
- Check if proper coolant is used
- Check if coolant is properly filtered
- Hole out of round
Hole out of size -
- Machining variable
-
- Select proper cutting feed rate
- Machine
-
- Make guide bush clearance closer
- Align spindle and guide bush more closely
- Tool
-
- Check if proper nose style is selected
- Coolant
-
- Select proper coolant
- Hole runout
-
- Machine
-
- Make guide bush clearance closer
- Align spindle and guide bush more closely
- Tool
-
- Check if proper nose style is selected
- Work material
-
- Check for blowholes or uneven wall thickness
- Check if the drill enters at right angle
CASE04Chip formation
Trouble
Cause
Countermeasure
- Clogged chips
-
- Low oil pressure
-
- Select proper coolant pressure
- Insufficient coolant flow
-
- Select proper coolant flow
- Check for coolant viscosity
- Poor chip formation
-
- Reduce cutting feed rate
- Select proper nose style
- Machine
-
- Employ larger chip box
- Entangled chips
-
- Stringy chips
-
- Increase cutting speed
- Check for excessive tip wear at outer corner
- Check for chipping at outer cutting edge or corner
- Check if grinding wheel grit is proper
- For stringy chips generated when drilling a guide bore, increase oil pressure and reduce cutting feed rate
- Bellow-like chips
-
- Check for chipping at apex point or its vicinity